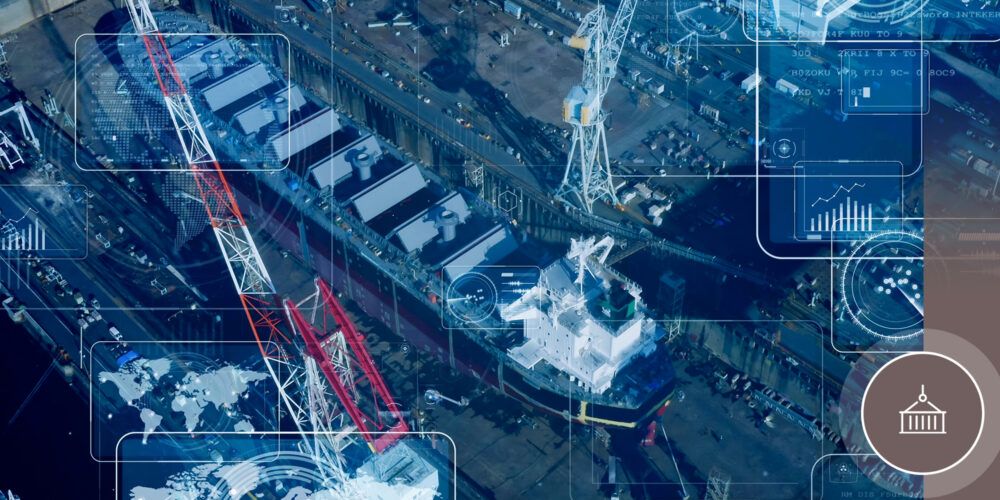
Automation of port terminals? Yes, but…
The added value that automation can bring to the international maritime and port sector in the context of efficiency and safety is something industry experts have become very aware of in recent years. But the challenges of automating container terminals are enormous. Tools such as digital twins help to increase efficiency and security, but the return in terms of productivity is not always "automatic" and the cost-benefits do not convince all ports.
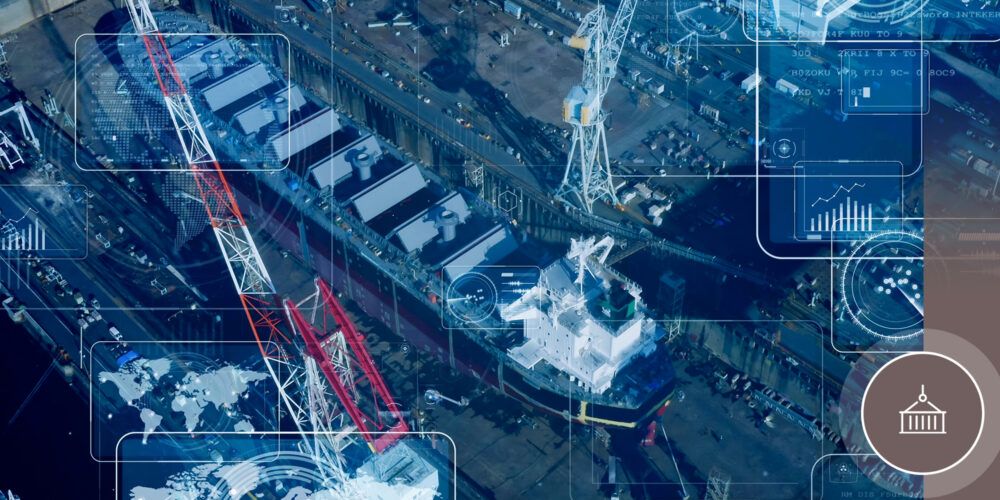
Automation across all port terminal areas is expected sometime in the next decade and a half. During a recent webinar session organised by CM Labs, experts in simulation-based engineering and training solutions, Laila El Moujtahid and Marc Desmonds spoke about what is triggering this seemingly unavoidable shift.
For El Moujtahid, a Senior Product Manager for CM Labs, investing in technologies “is the best way to remain competitive these days.”
She also emphasised that in an upsizing industry — today, 24,000 TEU vessels dwell the oceans and call the ports — there is no room for mistakes.
“Ports require thousands of people, computers and industrial machines to work together each day. So, making sure that schedules are met on time and without any incidents is a true challenge.”
Digital twins and algorithms
While confidence in automation technology is currently at its highest, some areas are lagging. Ship-to-shore cranes, for instance, are the least automated of equipment, but even these are predicted to embrace great technological advancements in the next few years – if not the greatest.
Desmonds, the founder and owner of MarCrane Port Equipment Consultant, thinks along the same lines as El Moujtahid when it comes to the critical level of precision required by the sector:
“The objective of automation is to minimise errors by reducing the human interaction in the process, to increase efficiency, to reduce the cost of operating a terminal, to increase safety, and, last but not least, to reduce the carbon footprint.”
Digital twin ecosystems, which use real-world data to predict how a product or process will perform, are a key element in the transition from manual to automated. The twins, as El Moujtahid explained, integrate the Internet of Things (IoT) and Artificial Intelligence (AI) to create a virtual replica of the real environment. The model consists of two parts: hardware and software. The former acquires and processes data; the latter represents and manipulates it. It “bridges the barrier between the physical entity and its representation.”
Emerging technologies, the IoT amongst them, encompass incredibly large amounts of data. Can they be managed at all? It is not impossible but certainly challenging. Traditional data management tools are no longer enough, which is why new sophisticated software that relies on strong AI and applies advanced algorithms is needed.
One of the main obstacles in automation is linked to the quality of the data exchange. A lack of structure and transparency often makes it hard to monitor the performance of the equipment. When data comes from several systems rather than one common, standardised infrastructure, the conditions for precise decision-making aren’t optimal.
A prominent threat in the context of data is cybersecurity. “Port stakeholders should have a good understanding of the type of data to share but also who to share it with, the value of this information, of the technology, and the impact on their businesses,” advised El Moujtahid.
Digital twin ecosystems, which use real-world data to predict how a product or process will perform, are a key element in the transition from manual to automated. The model “bridges the barrier between the physical entity and its representation.”
Automation = productivity?
According to a McKinsey report, “the top problem [with automation] is filling the specialized technical positions it requires... even experienced engineers can take as long as five years to train.” Productivity increases are thus not necessarily guaranteed. Terminals adopting automated processes have in fact reported declines in productivity, much of which can be attributed to training gaps.
Desmonds said that, for automation to truly result in a cost reduction, it is essential to make sure that candidates have the potential to become productive operators at the very early stages of the transition journey, and then, to invest in continuous training.
In the framework of full automation, the human factor remains indispensable, as “even in fully automated scenarios, there is some non-automated equipment.” Equipment operators are the ones ultimately in charge when things go wrong, or exception scenarios arise.
A challenging transition: security, the case of Auckland
The benefits of port terminal automation are clear: reduced costs per handled container, greater reliability, consistency, predictability, and security. However, the transition isn’t easy. An example of the difficulties that can be encountered during the automation process is the project of Ports of Auckland, New Zealand.
The plan to replace 50 stevedores with a fleet of 27 unmanned straddle carriers was unveiled in 2016. It was expected to be operational in 2019. Problem after problem, though, forced its delay and the project remains unfinished as of today.
The latest incident: a robotic transporter lost control and rammed a stack of containers. While investigators look into what went wrong, Auckland has resumed manual operations. Security goes above all.
The future of terminal automation for Barcelona’s Port Community
One of the topics experts from the Port Community discussed in workshops during the preparation of the IV Strategic Plan of the Port of Barcelona (2021-2025), which includes a Port Vision for 2040, was the future of terminal automation.
They concluded that the automation of container terminals will increase exponentially in the coming decades. However, despite its rapid growth, according to data collected by UNCTAD in 2018, only 1% of terminals are fully automated, while 2% are considered semi-automated.
Specialists estimate that, in the long run (2040), the increasing automation of terminals could end up turning them into commodities, making traffic between the different ports increasingly volatile. In addition, they highlight that automation occurs at the expense of flexibility – an element more and more necessary for ports in the wake of various disruptive events such as COVID-19 or the Suez Canal blockage.
An example of what can be achieved through a good transition is Hutchison Ports BEST in the Port of Barcelona. It is the first semi-automatic container terminal in the Mediterranean. It started operating in 2012 and has been improving its performance to reach more than 220 movements per hour and ship and more than 40 per hour and crane. Thus, thanks to its dimensions, equipment, workers and operating system, BEST is achieving one of the highest productivity in the world.
But there is the high investment cost of adapting these new infrastructures, which can be a barrier for certain ports.