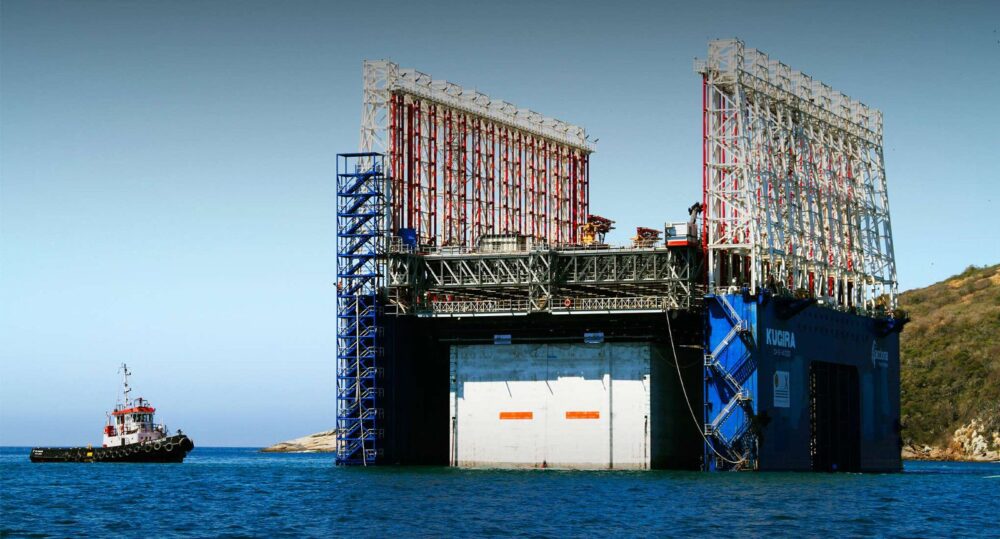
Kugira: The Floating Factory That Builds Docks In Record Time
Expanding the size and operating capacity of ports in record time with the minimal environmental impact is a true engineering challenge. One of the most advanced options meeting this challenge are floating factories or floating docks, like Kugira (from Acciona), which builds the gigantic blocks of concrete (caissons) that comprise the berthing lines in ports.
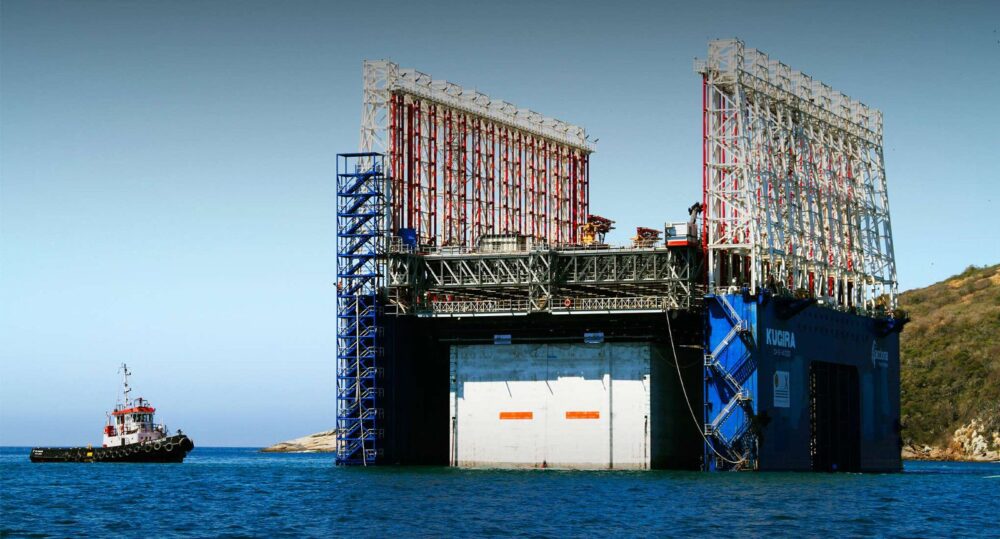
A ‘whale’ contributing to port construction
One of the largest caisson-building docks in the world is the Kugira (‘whale’ in Japanese). This herculean machine from ACCIONA measures the equivalent of an 18-floor building (56 metres tall, 74 metres long and 49 metres wide). A team of between 140 and 200 high specialised professionals work on the Kugira around the clock seven days a week, and it can manufacture concrete caissons weighing up to 24,000 tonnes. This means that it can create a seawall or a berthing dock 200 metres long from scratch in just one month. Despite its colossal size, the way this engineering whale works is based on simple principles. It begins by building the base (shoe) on which the caisson walls will be erected. The steel bar frame of this shoe is made on a flat floating surface (pontoons) on which the frame supporting the concrete is woven. To complete the assembly, it is placed on the floating dock and the concrete is poured. Once the concrete on the shoe is finished, the scaffolding is lowered, which acts as the mould for the walls, and the concrete is pumped in through three boom pumps fed by lorries which transport the concrete from the place where it is mixed. The formwork is slid using a system similar to the one used in bridge hoisting, which allows the walls to be filled with concrete without interruptions. This makes the sliding more precise, on the order of millimetres. Furthermore, the Kugira’s floating capacity allows it to dry-build a caisson measuring 18,000 tonnes.Adapting infrastructures to the new market demands entails a host of difficulties, such as the ever-changing conditions of the sea, interference with port activity and the environmental effects of building wharves and docks.
Advantages of caisson-building docks
The most obvious advantages are the speed and the reduction in the consumption of material. This means not only time- and money-savings but also a significant decrease in the amount of quarry materials required compared to other building techniques.- It is a highly versatile methodology since it adapts to the different ways the dock is used. “One good example is Port of Barcelona”, says Domingo González, Construction Director of the Business Unit Specialised in Ports and Hydraulic Works of ACCIONA Construction. “The extension of a dock for a cruise terminal was built, but if it has to be used for general cargo in the future, with everything this means in terms of larger overloads on the dock, the caisson will allow its use to be changed without having to change the infrastructure”. With a solution using piles, this would not be possible.
- Furthermore, since it works in the sea, the Kugira can be installed in a location where it does not interfere with port activity, so its economic activity is not harmed during expansion. Tugboats can take this colossal factory wherever it is needed.
- It can build longer caissons. “In Barcelona, the caissons are 40.3 metres, but we could have reached up to 66 metres. The largest caissons allow a large dock to be built in a single operation. In the case of Port of Barcelona, we manufactured a caisson every 7 days, and after a month we had 170 metres of dock. We finished the caissons in 49 days”, says Domingo González.
- Less quarry material is used than in a solution using piles because only the platform that serves as the base of the caisson is needed.
- Finally, “the caisson system allows for greater flexibility and provides better durability than what other structures can”, states Domingo González. They are reinforced concrete caissons, and while metal solutions usually require excess thicknesses or sacrificial anodes because they corrode, there are caissons from the 1970s which are still in perfect condition today.
The most recent work of the Kugira has been the enlargement of the Adossat dock in the Port of Barcelona, necessary due to the constant increase in the activity of the port.