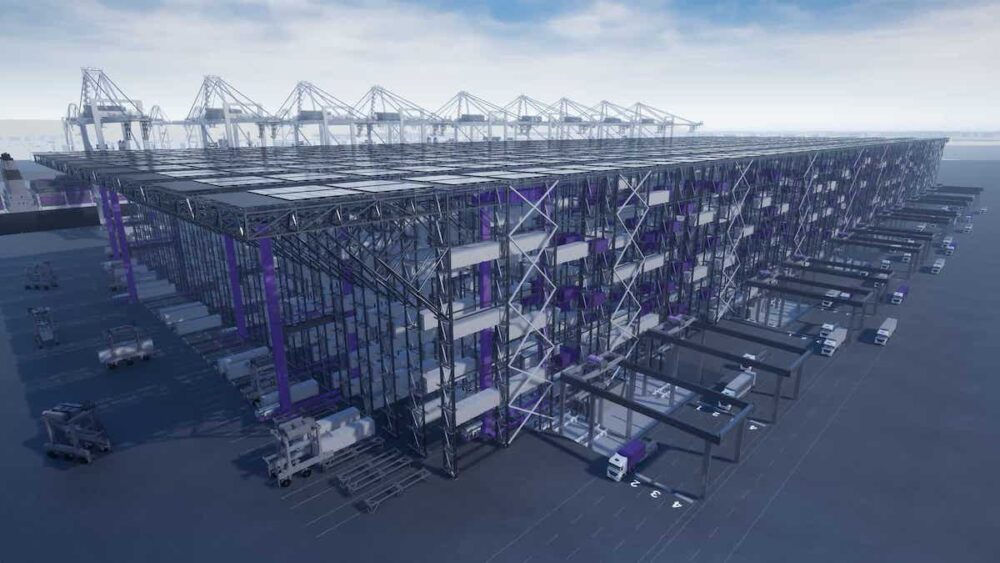
The past, the present and especially the future of automation in container terminals
Despite the fact that only 3% of container terminals are currently automated, ports are speeding up the automation process. This presents important advantages but also has some drawbacks that can make the speed of implementation vary depending on each port’s characteristics.
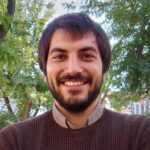
Javier Garrido is a researcher at the Center of Innovation and Transport (CENIT) and PhD student at Port de Barcelona.
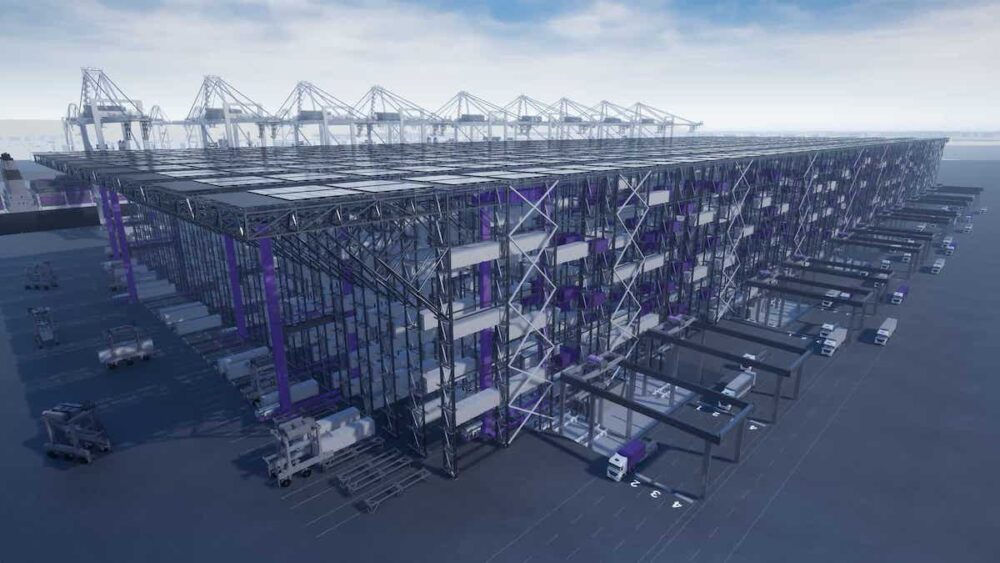
Automation feels radically new, but the truth is that the first automated terminals appeared in the 1990’s, such as the ECT Delta Terminal (HPH) of the port of Rotterdam. The following graph shows the evolution of the number of automated container terminals since their appearance until the present day. It’s worth noting that between 1990 and 2010 growth was linear, whereas during the last decade it has been exponential. Nevertheless, despite this strong technological push towards universal automation, a small decline can be observed in 2017, which may lead to a somewhat more moderate growth until 2030.
But what are we talking about when we talk about automated terminals? We currently distinguish between two types of automation:
- Automated terminal: port container terminals that have automated all yard and yard-dock movements.
- Semi automated terminal: terminals where yard movements are automated but yard-dock movements are done by conventional means or vice versa.
It is important to highlight that these definitions don’t take into account certain degrees of automation such as, for instance, access gates to the terminal, through which trucks are received and delivery control operations are managed; automation is a key factor for speeding up the logistics chain.
According to data collected by UNTCAD (2018), only 1% of port terminals are fully automated and 2% are considered semi-automated.
The following graph shows the distribution of semi- or fully automated terminals by country. Australia heads the list, as three of its six terminals are fully automated. In second and third place are the Netherlands and South Korea, with four terminals each. It’s important to note that the Netherlands’ four terminals, located in the port of Rotterdam, are all fully automated. This means the Netherlands is the leading country in Europe and the world.
Since 97% of port container terminals are still manual, what does the future hold for automation?
Some of the reasons that motivate automation of container ship terminals are:
- The appearance of mega ships: nowadays, container ships have grown up to 24,000 TEU capacity, which leads to demand peaks that have to be mitigated with optimal, streamlined logistics chains, making automation indispensable.
- When a terminal is in a geographic location that makes it difficult to expand.In these cases, automation is a key strategy for improving performance, streamlining processes and increasing competitiveness.
- When a terminal is a transhipment hub, automation is essential to increase the performance and efficiency of movements.
- Automated terminals equipped with the latest technology attract more clientele, as their operations are optimal and traceable. This adds value to the passing of goods through such ports.
Feedback from automated and semi-automated terminals in recent decades has been positive, because in most cases they allow higher and more regular gross productivities than manual terminals (Yang and Chen, 2013).
The main advantages of automating port container terminals include the reduction of costs per handled container, as long as the traffic volume is high enough to cover the investment costs. What’s more, automation also increases the reliability, consistency, predictability and security of port operations. From an environmental perspective, automation also has a lower environmental impact thanks to the optimisation of certain transactions.
However, certain investigations that analyse container movements per hour in European terminals cast doubt on the claim that fully automated terminals are more productive and cost-effective than semi-automated ones. For example, Barcelona’s semi-automated terminal, known as BEST, isn’t 100% automated and is yet highly efficient. Since it was put into service in 2012, the facility has steadily improved its performance. It is now one of the most productive terminals in the world, with more than 220 movements per hour per ship and more than 40 per hour per crane.
On the other hand, an investigation by CENIT Science for Transport concluded that automated guided vehicles (AGV) are only more cost-effective for port terminals with high labour costs and traffic volume of more than 100,000 containers per gantry crane per year.
The following diagram shows which port terminal automation technologies are consolidated, spreading or being adopted (Geography Transport Systems, 2019):
The future of the automation of container yards
Modern technology and the 4.0 digital revolution are bringing about tools that can improve the automation of terminals, among which are the noteworthy automated container yards with bay systems known as Boxbay. This project, designed by DP World and SMS Group, is regarded as a disruptive element for the future of port terminals.
Boxbay offers different solutions for storing and handling containers using a system known as High Bay Storage (HBS). This disruptive technology will significantly improve operations in container terminals. Instead of stacking containers one on top of the other, as has been done for decades, this system places each container on its own platform, making all containers directly accessible. In fact, this system adapts the concept of automated storage, which has been used for a long time in the field of internal logistics, to the port environment.
For terminals in gateway ports, characterised by their large number of import or export cargo operations, this degree of automation could be especially useful for optimising operations. By being fully automated, each and every container can be accessed individually, which avoids inefficient repositioning.
It also offers significant advantages such as increased movement speed, energy efficiency, security and, above all, a considerable reduction in operation costs.
The future of railways in automated terminals
One of the weakest points of terminal automation are rail freight operations. The main problems for automating combined railway transport are:
- The impossibility of combining manual and automated horizontal transport flows within terminals.
- Containers that are to be imported or exported by railway should be above the yard blocks reserved for them. Otherwise, moving them would accrue considerable extra charges.
The Boxbay system could solve these problems, as it would avoid interferences between the automatic and manual modes if a load line is reserved for such a purpose. Furthermore, having instant access to all yard containers would avoid the complications of preparing separate blocks for road transport and railway transport.
An increase in ship-freight intermodality would be of great socio-economic benefit thanks to the lower number of externalities this would involve when compared to road transport alone (Handbook on the external costs of transport UE, 2019).
What will automated terminals looks like in 2040?
Given the speed of technological progress and that the construction of new terminals lasts between ten and twenty years, the ones we will see in 2040 could have the following features:
- Automated dockside gantry cranes
- Automated container yard with bays
- Automated horizontal transportation
- Automated mooring system
- Automated terminal access gates
- Track&Trace for containers
- Infrastructure to accommodate both automated and manual trucks simultaneously
All these details will make the container terminals of the future more efficient and environmentally friendly than the ones we have today.
The downside of automation
The ever-increasing automation of terminals can end up turning them into commodities, making traffic more volatile between terminals and forcing operating costs to be an even more relevant factor than they are today. The cost of energy will then become an important factor in terminals where operations reduce labour considerably.
On the other hand, several experts claim that automation comes at the expense of the flexibility, which is increasingly demaned to ports. Addtionally, it can reduce a terminal’s ability to adapt to the growing demand of shippers in terms of service and response capacity. Fully automated machines can show little resilience when faced with disruptive events, making semi-automated options better for minimising risk.
Lastly, we can’t forget the high investment cost of adapting these new infrastructures and automated vehicles, which means we’ll need a socio-economic assessment to guarantee profitability depending on the expected traffic.