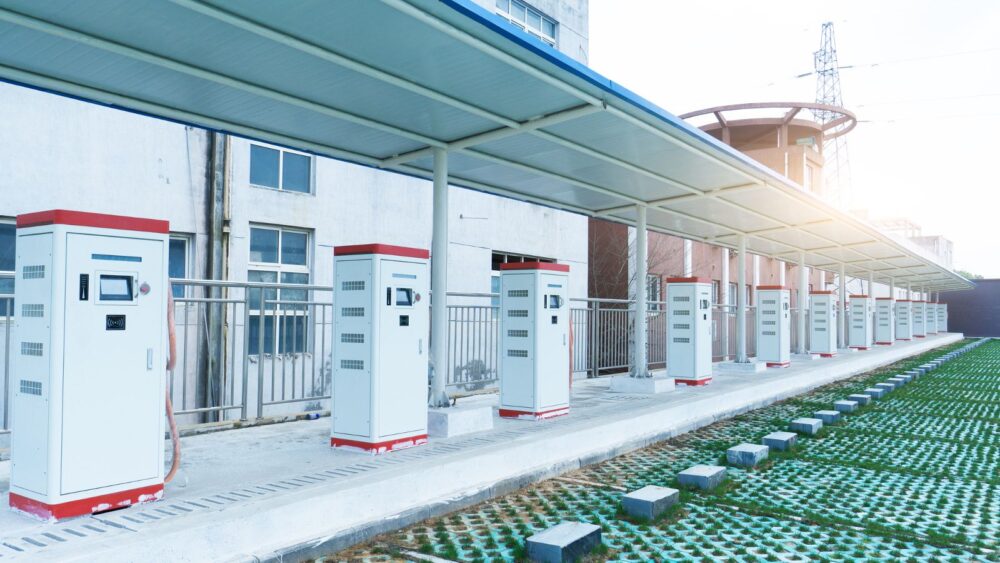
China Takes Control Of The Electric Vehicle
The pressure to cut contamination from private vehicles is mounting and electric cars seem to be the most viable alternative to this global issue. China has taken the lead, not only in terms of global production of the finished product but also in batteries and raw materials used for manufacturing. Where does this leave Europe and the United States in terms of leading this industry of the future? Here are some keys to the new map of power and interests regarding the electric vehicle.
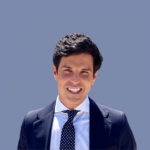
Carlos Martín is the Manager of the Ports and Maritime Transport Consultancy Area at IDOM.
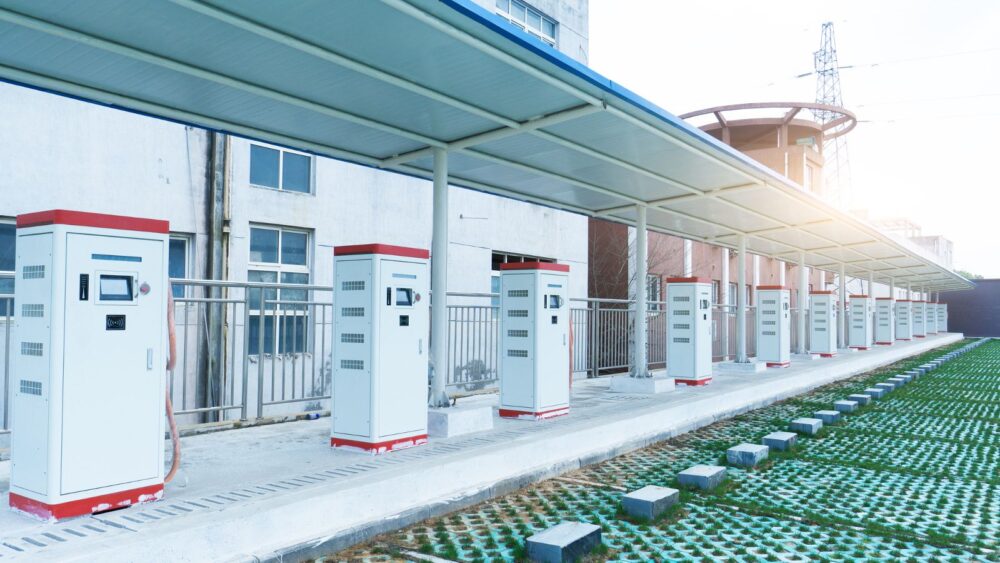
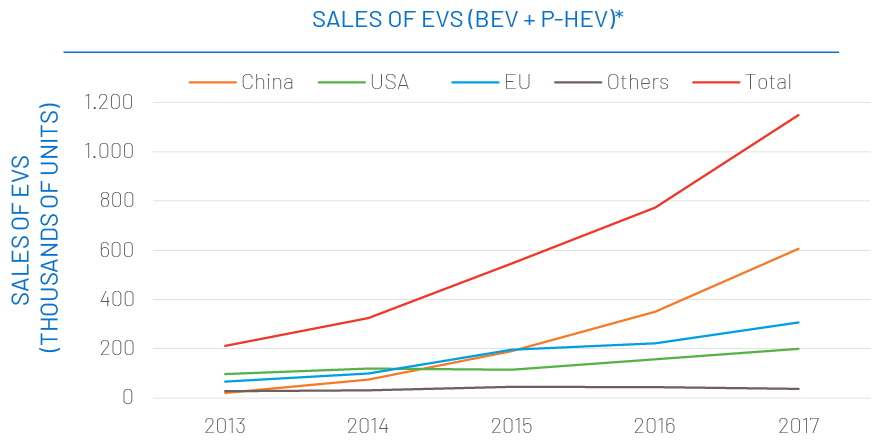
Light vehicles only. Heavy vehicles not included. Source: EV Volumes (The Electric World Sales Database) and CAAM (China Association Of Automoblie Manufacturers).
Plus, 606,000 electric vehicles made in China were sold in 2017, which accounts for 53% of the global market. Since 2013, the Chinese market has seen year-on-year growth of 733%. In 2014, China was already positioned as the top commercialiser of electric vehicles in the world, ahead of Europe and the United States. China's yearly growth, at a pace that its competitors can't keep up with, is down to several causes. Firstly, Chinese manufacturers are backed by the significant captive demand inside this Asian country. Plus, not only is the total volume of vehicles manufactured increasing, so is the range of models on offer. In 2017, Chinese buyers had 75 models of electric vehicles to choose from, more than in any other country.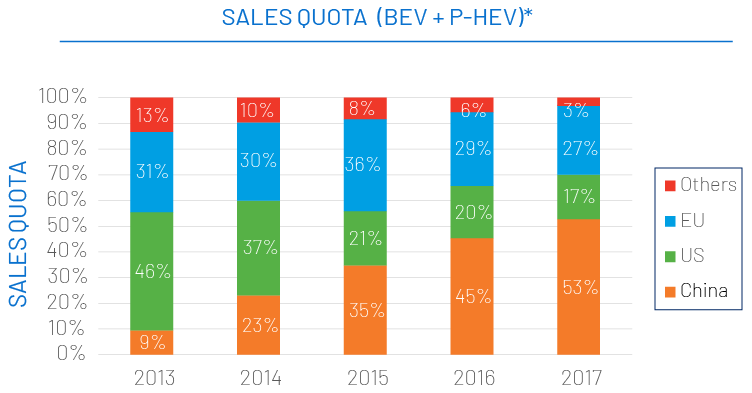
* Light vehicles only. Heavy vehicles not included. Source: EV Volumes (The Electric World Sales Database) and CAAM (China Association Of Automoblie Manufacturers).
606,000 electric vehicles made in China were sold in 2017, which accounts for 53% of the global market.
Batteries and power
The main limitation on the electric car market is the cost of batteries, which is about 30% of the vehicle price. Asian manufacturers have positioned themselves as leaders in producing and commercialising Li-Ion batteries. China, South Korea and Japan have 8 of the top 10 battery manufacturers in the world, which in 2016 were responsible for more than 85% of production worldwide. Specifically, there are 3 Chinese manufacturers among the top 5, including the number one company: CATL. In 2016, Chinese manufacturers produced more than 25% of the global capacity; in 2017 that figure was 55% and it is expected to be more than 63% by 2021. In 2016, there were 140 manufacturers of Li-Ion batteries in China.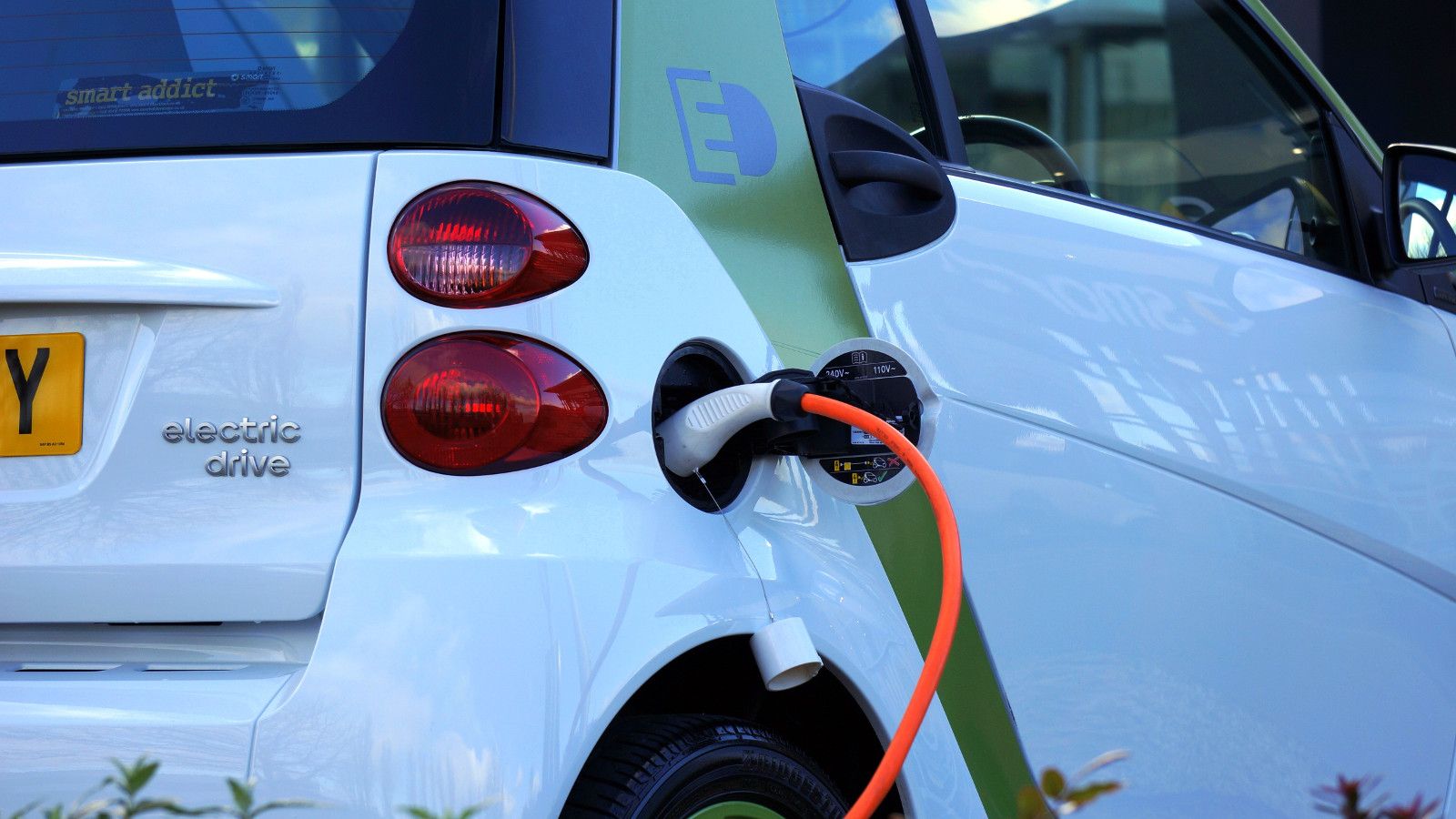
90% of electric vehicles manufactured in China used batteries from Chinese producers. [Image of Mikes Photos]
Demand to produce more and more
The off-the-charts growth in the production of Li-Ion batteries in China is down to two things. First, the government's strategy to promote battery production, imposing high production quotas on new companies looking to get into the national market. In 2014, China allowed national and international capital to be invested in battery manufacturers, which has fed the economies of scale and pushed down manufacturing costs. As a result, today China is the main supplier of batteries for electric-vehicle manufacturers worldwide. Secondly, and closely tied to the previous point, in 2016 approximately 90% of electric vehicles manufactured in China used batteries from Chinese producers. This means that the battery market needs the increasing demand for electric vehicles to stay afloat, and vice versa. This is the strategy both vehicle and battery manufacturers are using: by integrating both stages vertically, they eliminate the costs associated with spreading out the assembly process and get truly competitive end results.China, South Korea and Japan have 8 of the top 10 battery manufacturers in the world, which in 2016 were responsible for more than 85% of production worldwide.
The heart of the matter
To understand China's progress, we have to decode the international trade scenario for the raw materials used in manufacturing batteries over the past decade. Lithium, graphite, cobalt, nickel and magnesium are the main components of Li-Ion batteries. Both global demand for these materials and their price per tonne have increased considerably. In 2016, China was the leading importer of lithium, nickel, cobalt and magnesium, in addition to being the leading producer of graphite (used in the battery anode) in the world, with contracts in place securing the supply of raw materials to manufacture batteries for the next 5-10 years. The Chinese mining industry has seen a significant increase in activity over the past 10 years, over which time they have taken shares in foreign mining companies that operate in strategic locations. With the strategy of controlling the supply of raw materials to manufacture batteries, China is limiting real competition and access by battery manufacturers in the US (Tesla), Japan (Panasonic) and South Korea (LG Chem), among others.In 2016, China was the leading importer of lithium, nickel, cobalt and magnesium, in addition to being the leading producer of graphite.