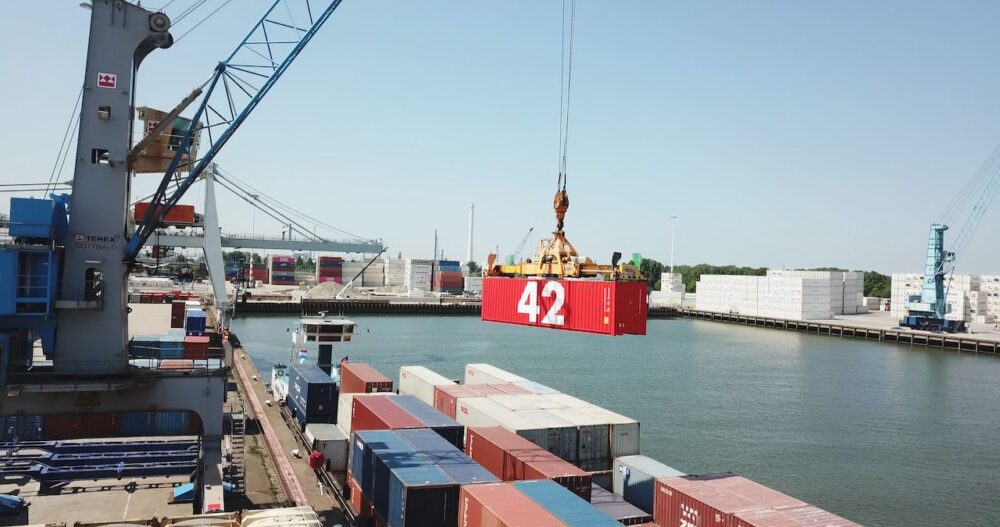
Will the unchangeable box ever change?
Shipping containers have remained virtually unchanged since they were standardised in the late 1960s and early 70s by the International Maritime Organization (IMO). Whereas shipping lines have substantially increased the size of their cargo carriers over the years, the industry has only made a few timid attempts to innovate in shipping boxes, mainly with foldable containers and smart containers.
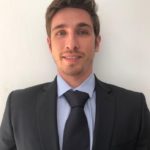
Tom Severijns works in the Department of Strategy and Innovation of the Port of Barcelona.
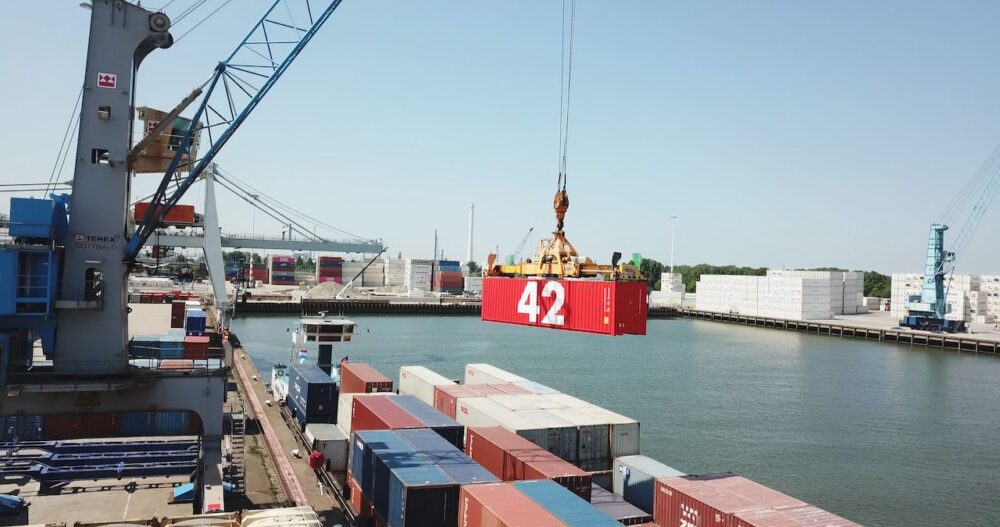
To date, transportation costs have been reduced mainly thanks to the economies of scale created by the shipping lines, in which container ships have grown from 1,000 TEUs in the 1950s and early 60s to nearly 24,000 TEUs in 2019. This phenomenon is also known as ‘gigantism in container shipping’.
One thing that has not changed in 50 years of maritime transportation, however, is the shipping containers themselves. Apart from being standardised by the IMO in the 1970s, shipping containers have remained virtually unchanged since they were introduced by Malcom McLean in the 1950s, when they were implemented for commercial use. McLean was an American transport entrepreneur and inventor who developed the modern intermodal shipping container as we still know it today. This led to a new term, containerisation, which is a system of intermodal freight transport using intermodal containers, also knowns as shipping containers or simply standard ISO boxes.
CONTAINERISATION: A DISRUPTIVE INNOVATION IN THE MARITIME LOGISTICS INDUSTRY
Containerisation brought about a significant cost reduction in the freight transportation industry as it eliminates the need for repeated handling of individual pieces of cargo. Not only did containerisation lower costs, it also improved transport reliability, reduced cargo theft and decreased inventory costs by shortening transit times.
Nevertheless, all these advantages also come with some disadvantages. The main disadvantage to the current standard ISO container is the elevated cost associated with empty container repositioning. Transporting empty units not only means high operational costs, it also decreases the available storage area on freight ships, meaning that fewer loaded containers can be shipped, which leads to elevated sunk costs and emphasises inefficiency.
Transport is a derived activity of the global economy, where trade volumes are determined by market forces. Trade patterns vary greatly based on geographical, geo-political, socio-economic and institutional relationships between countries. So, although transporting empty containers results in unproductive journeys, empty container repositioning is an unavoidable issue due to global trade imbalances.
So, if containerisation provides all the advantages mentioned above, but there are also some well-known persisting issues, why haven’t containers evolved and adapted to the current dynamics of the world’s economy?
Empty container repositioning is a persisting issue in the current global logistics supply chain, accounting for elevated financial and environmental costs
INDUSTRY ATTEMPTS TO GRADUALLY INNOVATE ON CONTAINERS
Some new concepts have been created, specifically foldable containers and smart containers. The idea of the foldable container arose in the mid-eighties and was created with the aim of reducing repositioning costs by folding the unit when unloaded. This way, the folded box takes up less space onboard the cargo ship. However, this concept has not been able to be implemented in the global supply chain due to certain technical difficulties these boxes pose and the elevated cost of using them in the logistics chain.
There is a trade-off between savings from using foldable containers and the costs they add to the logistics chain. The net result of the foldable container’s success depends on the time and costs involved with folding and unfolding, so it is essential to be able to fold and unfold cheaply.
Due to the structural and technical characteristics of a foldable container, the manufacturing costs are higher than for a standard box. Also, standard boxes have a higher comparative advantage in multi-trade operations, as their turnaround time is much shorter. This means higher productivity, which in turn leads to an increase in revenue. So, the manufacturing costs of a foldable container (purchase price) would have to be proportional to those of a standard one in order to be competitive.
Furthermore, foldable containers would also have to be compatible with the existing equipment for intermodal transportation in order to be able to compete with the standard ISO boxes. This means that the technical characteristics of a foldable container should conform to the norms and features of the standard ISO box, and have specific technical features to guarantee the system is technically efficient.
Some examples of foldable containers include 4FOLD in the Netherlands, ZBox in Spain and the Korean Railway Research Institute (KRRI). They usually offer a space reduction of 75% to 80% when folded, meaning that 4 or 5 folded containers take up the same space as one empty standard ISO unit. Moreover, operational costs can be reduced by 25% to 75% and CO2 emissions, by 20% compared to standard ISO containers.
Connectainer offers a different proposal: regular 20-foot boxes that can be conjoined to create a single 40-foot unit. All the required elements to join the boxes are kept inside for easy accessibility and storage of the parts needed, and it would only take about 20 minutes to join two standard 20-foot boxes to make a single 40-foot unit.
Each container has 6 electronic displays with an integrated chip that allows them to have a different numbering depending on their size (20 feet or 40 feet). The main concept behind this product is that you can connect two 20-foot containers to make one conjoined 40-foot unit. The opposite is also true; you can disconnect the conjoined unit in order to have two separate standard 20-foot boxes, hence the name Connectainer. When two 20-foot boxes are being joined to make one 40-foot container, the conjoined unit takes the higher unit number of the two and all displays will be instructed to show the single numbering for the 40-foot container.
The aim of Connectainer is to improve multimodal logistics through innovation, which would ultimately result in decreasing the transport of empty containers by adapting the size of the units according to the needs derived from trade flows.
Regarding smart containers, this is a relatively new concept as it integrates digitisation, AI, IoT, blockchain and robotisation. By involving digitisation throughout the supply chain, this would make it possible to track the location and movements of containers. So, a new concept of containerisation has emerged from the depths of the seas. Some examples include Container 42 or Zbox.
EXAMPLES OF SMART CONTAINERS
Container 42 claims to be able to record its location and status at all times, including climate conditions inside and outside the container (humidity and temperature), the closing or opening of the unit, vibrations, inclination, position, sound and air pollution. It also features a variety of cameras that take time-lapse images or start recording during specific events (e.g. when the container is opened). It is also equipped with solar panels that measure how much energy it can harvest during the entire journey in order to be self-sufficient.
The “We Are 42” project is an initiative of the Port of Rotterdam that has developed the Container 42 concept. Moreover, this smart box is equipped with sensors that collect data throughout the supply chain. The collected data aims to improve operations in the logistics chain in order to make the entire process more efficient and seamless. Keeping track of the progress of the containers anywhere in the world allows for enhanced equipment and stock inventory planning, leading to a reduction in costs. Moreover, this project also intends to decrease ecological footprint for more sustainable globalised maritime trade.
The IMO estimates that carbon dioxide emissions from shipping in 2012 made up 2.2% of all human-made emissions worldwide, and this will rise 50% to 250% by 2050 if no actions are taken. Therefore, by further automating international shipping and even making it fully autonomous in the future, we can expect to drastically reduce the emissions of harmful substances.
This smart container is currently being pilot tested on a 2-year voyage around the world to collect data. It left the Port of Rotterdam in June 2019 and will visit several partner ports to showcase this new concept. It will be collecting data at the same time, which will later be analysed to see how digitisation could benefit autonomous shipping and to enable ports to undergo a digital transformation (for example developing a so called ‘digital twin port’).
Zbox, in addition to being a foldable container, it also integrates IoT sensors, AI, Big Data and blockchain. It complies with the ISO container standards in terms of technical features and can also be easily folded/unfolded. When the box is empty, it can be folded, taking up 80% less space. This means that one standard ISO container (unfolded) equals 5 folded containers in terms of space.
WHAT CAN WE EXPECT TO HAPPEN?
Will the future lie in both foldable and smart containers? Or maybe a combination of the two?
These questions cannot be answered yet, as the foldable containers haven’t been fully implemented in the logistics chain, because further technological advancement is required, mainly in two areas. The first area would be the product itself. Economies of scale would need to take place in order to make the purchase price more affordable to compete with the standard ISO units. Moreover, many moving parts from a foldable container are not as reliable and prone to malfunction. The second area is regarding its integration into the logistics chain. The whole supply chain would need to be adapted in order to efficiently process the flow of foldable containers, to be able to fold and unfold the units quickly and cost effectively.
The smart container is currently being pilot tested, so we can’t yet comment on the commercial feasibility or applicability of this product in the market, as this concept is still in the research phase.
Therefore, we cannot expect a disruptive innovation in this industry, as shipping lines and port terminals have invested heavily in the current business model, assuming that the container would remain the same for the foreseeable future. We could, however, expect some incremental innovations where foldable and smart containers might find their niche in the market.
Lastly, as a final remark, transport is a derived activity of global market supply and demand. This means that fluctuations in cargo ship traffic are fundamentally dependent on the global economy. When certain innovations take place, we also need to consider economic variables and not only technological ones. A new application might be technically feasible, but not commercially applicable for a certain process enhancement, in this case the global supply chain, or due to overall profitability or sustainability.