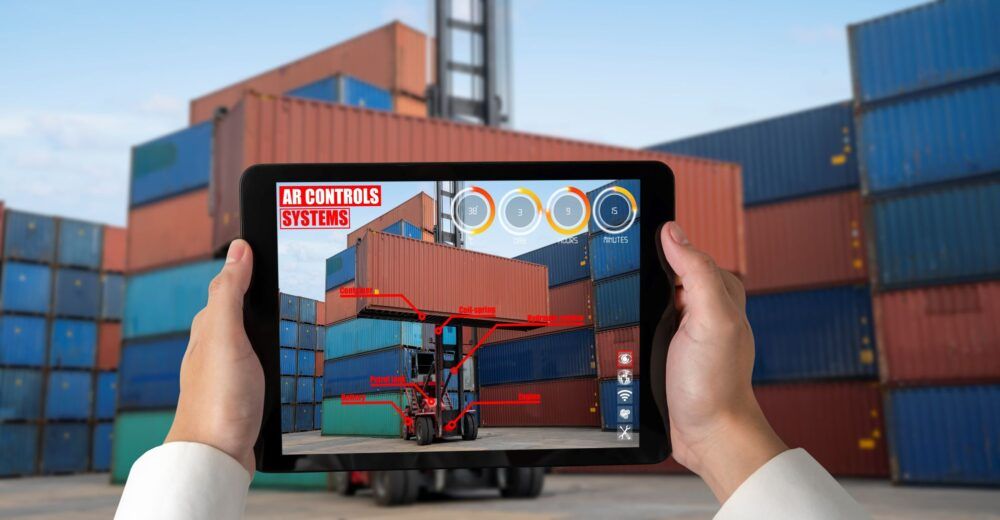
The progress of ports towards an Industry 4.0
Although the port sector has not been a great pioneer in automation and digitisation, in recent years it has strongly embraced these concepts. While initially the focus was on improving production, a broader objective should not be ignored; that of Industry 5.0, a concept that involves thinking beyond business results to maximise the health of the planet.
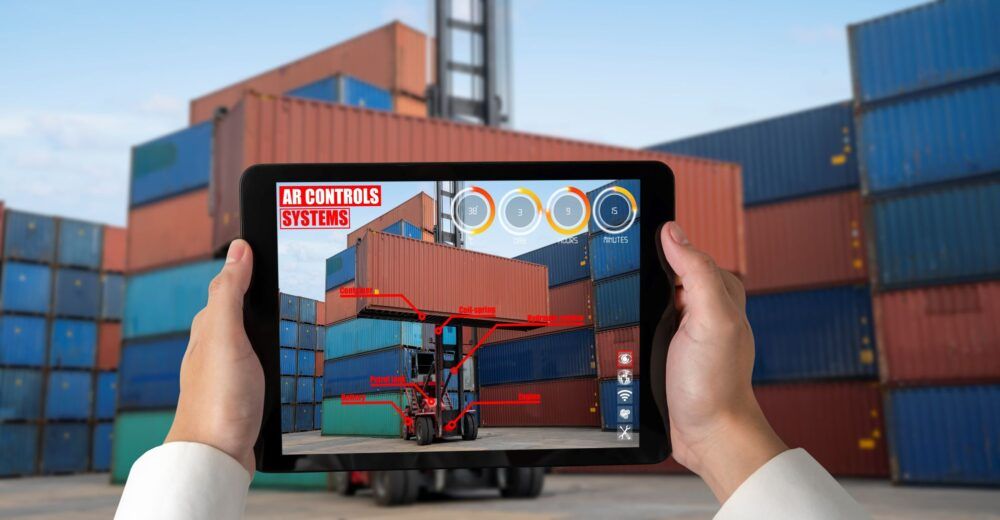
In the industrial sector, the process of digital transformation is called Industry 4.0, where 4.0 refers to the fourth industrial revolution.
- The first industrial revolution took place in the 18th century. Mechanical production equipment powered by water or steam started to be used.
- The second industrial revolution started at the end of the 19th century. It was based on mass production, the division of labour and the use of electric power to drive production machinery.
- The third industrial revolution was based, from the 1970s onwards, on the use of electronics and computers to automate production.
- The fourth industrial revolution, or Industry 4.0, is based on the use of interconnected and networked physical and cybernetic systems and the convergence of numerous information and communication technologies.
"As a term, it was made official in 2011 and its full implementation is planned for 2040, when it is estimated that society will be completely digital," says Xavier Pi, co-director of the Industry 4.0 Master's programme at the Universitat Politècnica de Catalunya and member of the Industry 4.0 Commission.
The fact that we are talking about an industrial revolution does not only imply a set of technological advances, but a "revolution", a drastic change in the ways of working that will have a global impact on society as a whole, in the same way as the appearance of the steam engine, electrification and assembly lines or computers did in previous industrial revolutions.
Port and Industry 4.0
For Pi, the port sector is a pioneer, in many respects, in the incorporation of these ideas. At the end of the 20th century, the emergence of PCS (port community systems) solved the needs of the sector's agents to interconnect with each other. Today, these systems have matured considerably and talk of digitalisation and automation is commonplace in port activity.
Despite this natural evolution, the ports and the public administrations on which they depend are making a firm commitment to accelerate these processes. Proof of this are the subsidies that exist to digitise processes and operations, such as the Ports 4.0 Fund.
Ports are incorporating aspects of Industry 4.0 in a natural way. For example, the Automatic Identification System was implemented years ago to identify the position of ships, but now technology allows us to go much further.
“The 5G Maritime pilot at the Port of Barcelona is a more sophisticated evolution based on IBM technology, high-resolution cameras from Huawei and Vodafone's 5G network, which enables high-precision geolocation using images and artificial intelligence," says Pi, referring to the pilot report produced by Mobile World Capital.
Thanks to their high connectivity, low latency and wireless nature, 5G networks will make it possible to deploy and connect all kinds of devices and run virtual models. "Digital twins themselves are connectable components, just like machines, systems or sensors. The Internet of Things will lead us to a scenario in which any element can be connected and this is very important," he says.
In other fields such as automation, other ports have also initiated projects linked to Industry 4.0. Singapore is applying this in the Tuas Megaport project, which will become the largest fully automated port in the world once the model is extended to the rest of the port areas in 2040.
This automation will occur at various levels; from cranes and cargo containers to autonomous vehicles managed by an intelligent control system and remotely. Thus, thanks to technology and interconnected systems, aspects such as safety, sustainability and productivity will be improved.
In 2019, the Port of Rotterdam initiated with IBM the development of a digital twin of the port, and in 2020, the Port of Los Angeles and IBM reached an agreement to create a cyber resilience centre to reduce the risks of cyber-attacks on cargo and information exchange. The port is also working, in collaboration with General Electric, on the creation of a digital platform called Smart Port with the aim of improving the planning and efficiency of the supply chain.
Finally, the port of Hamburg, which has, among others, an IoT project to track different types of pollution, including marine noise. It also employs smart solutions in operations such as security, real-time navigation and maintenance operations.
Industry 4.0 is not just a set of technologies but a "revolution", a drastic change in the ways of working that will have a global impact on society a whole
Why are we heading toward digitisation?
Between the late 19th century and the 1960s, production systems produced large volumes of standardised batches of products. From the 1970s and 1980s onwards, production lines began to produce customised and tailored product ranges, requiring greater flexibility that can only be achieved, in Pi's words, through digitisation. Today, with the rise of e-commerce, consumers demand unique or highly customised products and immediate or personalised delivery.
"Thanks to digital twins, there is no longer a wall between analogue and digital. It is possible to digitise physical assets by creating a digital interface, which could be described as a 'digital bell', allowing reality to be integrated with modelling, and processes to be tested, developed and simulated with lower risk and greater accuracy. This digital asset then returns to the physical world, to materialisation, with the experience learned at the digital interface,' he says.
Advantages of Industry 4.0
In addition to facilitating the simulation of products, services and processes in safe environments, Industry 4.0 enables:
- Predictive maintenance. The combination of technologies such as the Internet of Things, the cloud and artificial intelligence makes it possible to monitor the continuous, real-time operation of industrial machinery. This makes it possible to anticipate malfunctions and avoid production stoppages.
- Automation: The aforementioned technologies also make it possible to automate processes, with the advantage of reducing errors and increasing efficiency.
- Sustainability. The possibility of designing future predictive models and the collection of past information makes it possible to synchronise and monitor all this data in order to optimise environmental and economic resources and reduce waste.
- Transparency. Another key technology in Industry 4.0, in this case the blockchain, allows traceability and decentralisation in the transaction of data and operations.
At what stage is Industry 4.0?
Xavier Pi explains that there are several phases of implementation. "At the moment, companies are in the third phase of the Acatech maturity model (of a total of six), creating digital data repositories, the so-called 'digital shadows'. They are putting sensors in place, capturing and accumulating data.
The fourth phase is to identify what data is valuable, "separating the wheat from the chaff." The next is to clearly understand the conclusions that this data yields. This, Pi says, means "understanding the processes".
At a more advanced stage, predictive simulation models begin to be generated for trial and error in digital environments. The last stage is full automation.
THE ACATECH MATURITY MODEL
"More and more products related to these technologies and solutions for the digital twins are appearing on the market. In artificial intelligence, for example, there is now talk of 'explainable AI', and therefore interpretable and judged. AI algorithms are like a black box and there are techniques and analyses to check if their diagnosis is biased," he explains.
The expert adds that there is still a long way to go and to fit this series of solutions in an integrated way.
Boston Consulting Group, for example, launched in 2015 a model with the nine technological pillars of Industry 4.0.
THE NINE TECHNOLOGICAL PILLARS OF INDUSTRY 4.0
A change of mindset and Industry 5.0
Xavier Pi slips two concepts derived from Industry 4.0 that should be taken into account:
- The metaverse: "which is taking this idea to the limit. Creating a virtual world where you can test and make mistakes, at a much lower cost, with the aim of applying these changes in the real world. This is a very profound revolution," he says.
- Industry 5.0: "a concept born in Japan that applies the same technology as Industry 4.0 but with a different purpose. While 4.0 focuses on the business sector, this new concept has a planetary discourse, maximising the health of the planet," he says.
Unlike a few years ago, the technology that makes Industry 4.0 possible is already here. The main barrier to overcome, Pi points out, and which is the first obstacle often identified, is the lack of digital mindset. When in a couple of decades a majority of society becomes digitally native, Industry 4.0 will be fully materialised.