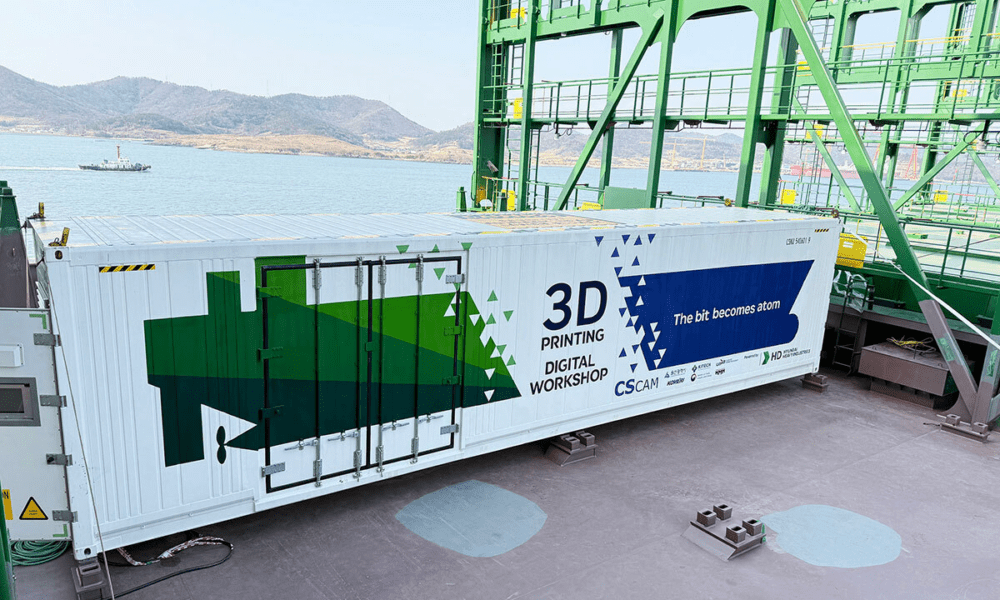
The use of 3D printing in merchant shipping
The use of 3D printing in shippingOnboard 3D printers offer an advantage for shipping: they facilitate the availability of parts and make maintenance operations cheaper. A horizon of opportunities that is welcome in a context marked by some uncertainties for international shipping.
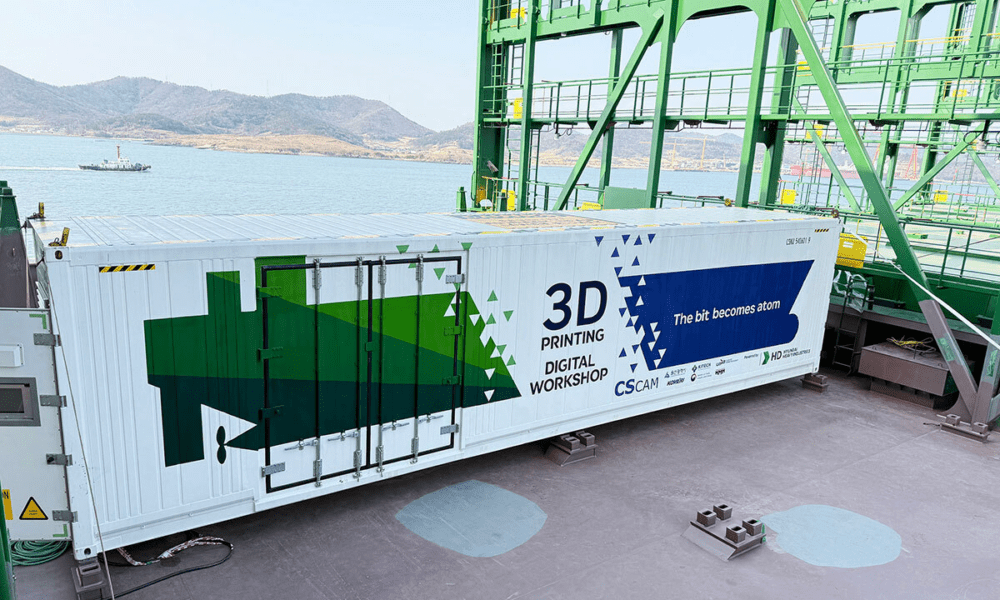
3D printers on board
In mid-March 2025, Korean shipping company Hyundai Merchant Marine (HMM) announced that its container ship HMM Green underwent trials to demonstrate the effectiveness of its onboard 3D printing system. Having this capability on a ship means being able to manufacture components needed for spare parts. It is the world's first commercial vessel to have a 3D printing center specially designed for maritime work.
As HMM announced, this technology allows them to produce essential stainless steel components directly on the vessel, which significantly reduces lead times and minimizes inventory costs.
“A major turning point for 3D printing in the maritime sector,” is how Forbes magazine described the South Korean shipping company's breakthrough. In a sign of what this initiative implies for shipping. Of course, the news also attracted the attention of specialized publications that took notice of the innovation brought by HMM.
If a ship like the HMM Green has 3D printing - or Additive manufacturing, if you prefer a more technical term - on board, a number of advantages are achieved in the operation of the ship. The main one is to achieve the advantages of the on-demand concept at its maximum level: spare parts will be available in a short time and just when they are needed, without having to rely on supply chains from a port.
The Additive manufacturing equipment on board HMN Green is known as the 3D Printing Digital Workshop. Until now, the conditions of any navigation - conditioned by winds and sea currents - made it doubtful that these printing devices would work properly in a sea moved by complicated weather.
Hyundai Heavy Industries took up the challenge and, with support from the South Korean government, began in 2023 to develop a 3D printing unit that could operate on board a ship, regardless of sea conditions. The solution was to install an additive manufacturing system inside a shipping container. The printing device has a proprietary motion compensation system that avoids problems caused by the rocking of the ship.
3D on board also in the military navy
The case of the HMM Green was the first among merchant shipping but several military navies already have experience with 3D printing on board. The US Navy installed the first Additive Manufacturing system on the amphibious assault ship USS Essex in 2022. A year later, a similar ship, the USS Bataan was able to repair a problem with its air compressor at sea.
Also in March 2025 although not an onboard device, it was announced that the new aircraft carrier USS Enterprise will feature a manifold created with 3D printing.
Another example of a military navy that has resorted to onboard 3D printing is China's navy. Although the People's Republic is wary of disclosing military matters, it was reported in January 2025 that a Harbin destroyer was able to repair its broken engine using these methods while operating in the Arabian Sea hundreds of miles from its bases.
In Europe, the British and Dutch navies have announced their intention to rely on 3D printing devices to improve their operational capabilities by reducing costs and streamlining logistics processes.
Additional advantages of on-board 3D printing
This ability to produce the necessary spare parts on board just when they are needed is especially advantageous for vessels operating on very long routes. It should not be lost sight of the fact that many merchant ships now operate on longer routes due to the traffic problems seen in recent years in some key waterways such as the Suez and Panama canals.
Collateral benefits include reduced inventory costs and reduced downtime during ship repair, to name two of the most obvious. For example, according to HMN's own data, the waiting time for a part is reduced from 233 days to just 48 hours (the time it takes to produce with printing).
3D in the maritime sector is not that recent
3D printing in the maritime sector has at least a decade of history. Until now, Wilhelmsen (in a joint venture with Thyssenkrupp) had been the big mover in this method of manufacturing spare parts at its Additive Manufacturing site in Singapore. From there, it transported them to the ships that needed them and sailed close to the coast.
Maersk Tankers also has more than a decade of experience manufacturing spare parts such as engine components with 3D printing. In 2014 it also conducted trials on board one of its container ships also with the aim of eliminating costs of storage and more complicated issues for the logistics of a repair such as bringing the new part to the port and chartering a delivery vessel.
Another option is to use 3D printing in repair vehicles. This is the proposal of the Norwegian company Kongsberg Ferrotech. They have a robot, Nautilus, with Additive Manufacturing technology that can repair metal structures underwater. It is also suitable for installations such as hydrocarbon extraction platforms, as it can operate at depths of up to 1,500 meters.
Standards for on-board 3D part validation
Classification societies are also taking the issue seriously. The American Bureau of Shipping has been working for years to establish standards to validate the many spare parts for ships that can be produced with additive manufacturing. Lloyd's Register has also undertaken similar certification work.
According to a study conducted by Lloyd's Register itself, the adoption of 3D printing in the marine sector could reduce delivery times by 40% and the costs of transporting spare parts in shipboard inventory by 50%.
3D printing also offers possibilities to rationalize the consumption of materials for the production of parts - being on demmand the production is adjusted to the need.
By creating spare parts perfectly adapted to the needs of the vessel, it is possible to optimize their weight, which, together with the rationalization of cargo in the holds (it is not necessary to carry so many spare parts), can optimize fuel costs.